某公司4500t/d生產線使用的煤磨為Φ3.8m× (3.5+7.5)m球磨機,在生產過程中遇到了一些問題,經采取Y效措施,煤磨生產狀況得到了G善,同時提高了臺時產量,降低了電耗。
一、工藝流程和主機配置
熱風取自窯尾,在高溫引風機前設置有S筒旋風除塵器,收集窯尾回灰中的生料粉,出磨設置1臺粗粉分離器和1臺細粉分離器,Z后經袋除塵器收塵,袋除塵器下設置2列FU拉鏈機,成品煤粉經拉鏈機入螺旋輸送機,通過螺旋輸送機正、反轉分別入窯頭、窯尾煤粉倉。煤磨系統(tǒng)工藝流程見圖1,煤磨主機配置情況見表1。
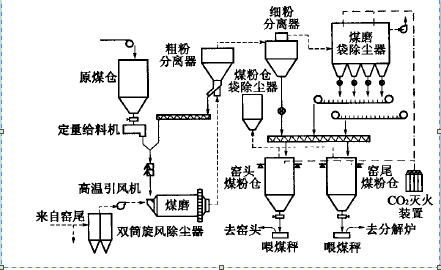
圖1 煤磨系統(tǒng)工藝流程
表1 煤磨主機設備配置
二、S筒旋風除塵器下料的改造
2.1 改造原因S筒旋風除塵器收集的細粉一側直接入大拉鏈機與增濕塔回灰一起回生料均化庫,另一側經一個小拉鏈機再入下部大拉鏈機后與增濕塔灰一起回庫,見圖2。經分析,鑒于現場高度有富余,該處粉狀物料的水分小,顆粒細,流動性好,且該側旋風除塵器下料口與下部大拉鏈機的夾角大于50°,所以,物料完全可自動流入下部的大拉鏈機。
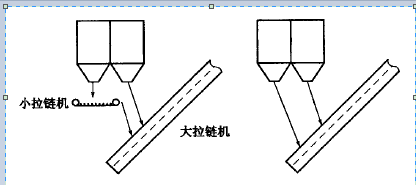
圖2 S筒旋風除塵器改造前后示意
2.2 措施
取消該處小拉鏈機,設立一個溜子使收集的細粉直接流入下部大拉鏈機中,見圖2。
2.3 效果減少1臺拉鏈機后,可節(jié)省1臺3kW的電動機;減少了生產環(huán)節(jié),降低了設備磨損與維護、維修費用。
三、煤粉入倉的改造
3.1 改造原因
出磨煤粉是經過粗、細粉分離器收集較粗顆粒后,再入煤磨袋除塵器收集,這樣煤磨袋除塵器收集的成品煤粉很細,經測定:當煤磨袋除塵器與細粉分離器混合的煤粉R0.08在3.5%~4.0%時,煤磨袋除塵器收集的煤粉細度只有0.5%。由于窯頭用煤粉較細,便于煤粉快捷燃燒形成高溫火焰,而F解爐只需要850~900℃的溫度用于碳酸鹽的F解,煤粉細度可以粗一些。鑒于此,考慮將煤磨袋除塵器收集的成品煤粉直接入窯頭煤粉倉,細粉分離器收集的煤粉直接入窯尾煤粉倉,可以滿足窯頭煤粉細、窯尾煤粉粗的需要。
3.2 措施
(1)在入窯頭煤粉倉的煤粉螺旋輸送機與窯頭煤粉倉入孔門接近的位置處,安裝一個帶螺旋閘板閥的溜子,將煤磨袋除塵器其中一側4個積灰斗的煤粉直接進入窯頭煤粉倉。
(2)為了防止入窯頭煤粉倉4個積灰斗的煤粉量不能滿足窯頭喂煤用量,再將入窯尾煤粉倉的煤磨袋除塵器另一側的2個積灰斗的輸送溜子都接人窯頭煤粉倉的煤粉輸送機(現場的高度、角度能滿足直接接入要求)。
3.3 效果
在保證窯頭喂煤的細度R0.08≤2.0%時,可以提高窯尾喂煤細度R0.08≤6.0%。由于煤粉細度放粗,不但有利于窯的煅燒,還可以提高煤磨產量,從而降低電耗。
四、煤粉螺旋輸送機的改造
4.1 改造的原因
原有的煤粉螺旋輸送機設置3節(jié),每節(jié)之間的連接使用輸送機軸、竄釘固定連接方式,一旦竄釘因脫絲或老化斷開進入喂煤秤內,將喂煤秤卡死,處理一次Z短時間3h,即影響回轉窯運轉時間3h。
4.2 措施
使用原有的煤粉螺旋輸送機殼體,更換為整根的螺旋輸送機軸。
4.3 效果
(1)減少螺旋輸送機竄釘因脫絲或老化斷開維修,降低了維修費用。
(2)減少了2套吊瓦架裝置,按照1套吊瓦架裝置使用期3個月,每套費用按2000元計算,每年節(jié)省費用16000元。
(3)避免了竄釘因脫絲或老化斷開進入喂煤秤內而將喂煤秤卡死的現象。
五、煤磨磨尾螺旋筒的改造
5.1 改造的原因
煤磨正常生產,班班都出現磨尾漏煤現象,少者1t,多者3~5t,浪費人力、物力進行清理,影響生產。根據煤磨工況,從煤磨鋼球級配、煤質等方面考慮,認為是磨尾螺旋筒輸送問題,螺旋葉片高度較低,出磨煤粉不能及時輸送,從磨尾沿密封處冒出。
5.2 措施
將煤磨磨尾螺旋葉片高度由60mm提高到80mm。
5.3 效果
(1)煤磨臺時產量由42t/h提高到45t/h。
(2)技改后沒有再出現磨尾漏煤現象,避免了煤磨因漏煤造成的環(huán)境污染,節(jié)省了人力、物力。
六、煤粉倉袋除塵器的改造
6.1 改造的原因
窯頭煤粉倉、喂煤秤和窯尾煤粉倉、喂煤秤共用1臺小型袋除塵器,2個煤粉倉和2個喂煤秤收塵管道設置均為“2合1”,因此易出現窯頭、窯尾煤粉倉下煤不均勻,兩倉煤粉有“竄倉”現象。經現場勘查證實,2個喂煤秤通過共用袋除塵器“2合1”收塵管道竄煤,直接影響煤粉均勻入倉和煤磨高峰電避峰時間。
6.2 措施
根據現場地理位置,把窯頭煤粉喂煤秤和窯尾煤粉喂煤秤收塵管道分成2路各入各煤粉倉,再入袋除塵器,煤粉倉和喂煤秤收塵管道改造前后見圖3。
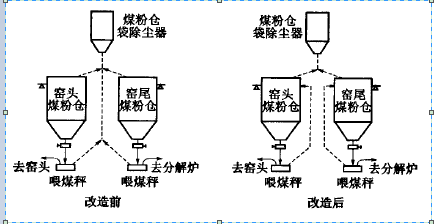
圖3 煤粉倉和煤粉秤收塵管道改造前后示意
6.3 效果
(1)將2個喂煤秤收塵管道分離,杜絕了煤粉“竄倉”現象。
(2)合理調節(jié)煤粉均勻入倉,延長煤磨高峰電避峰時間。
(3)根據窯況需求,分別調節(jié)窯頭、窯尾倉煤粉細度,從而提高煤磨臺時產量,降低電耗。
七、改后效果
該公司通過對煤磨系統(tǒng)的一系列改造,煤磨臺時產量由原來的
42t/h提高到46t/h,電耗由原來的36kwh/t降到34kWh/t。
|